Construction Labor Shortage
A shortage of skilled construction labor has been a persistent issue in the United States since before the pandemic. In fact, it is rooted all the way back to the Great Recession. Regardless of industry segment, every company has been trying to find solutions to the problem. The construction industry has not been immune to the problem of labor shortages.
Companies looking for labor have made efforts to attract new hires, e.g., increases in base wages, more flexibility in benefits, sign-on bonuses, but the problem persists. One area that goes unnoticed is efforts related to the application of lean methods in the construction industry.
The North American automotive industry embraced the discipline of lean manufacturing, i.e., the reduction and/or elimination of 8 wastes, in response to market share losses to Japanese automotive imports. By methodically and repeatedly reducing or eliminating non-value-added steps in the business processes, the Japanese realized sustainable improvements in costs, quality, and profitability. Many organizations have adopted the Toyota Production System (TPS) considered the benchmark of lean implementation.
Lean manufacturing is not a discipline designed to eliminate labor but instead makes the best use of available labor and other resources. Companies that implement lean find that they realize gains in output and capacity with their existing resources. And a lean company is in a better position to weather a tight labor market than a non-lean company.
The construction industry began to implement lean techniques in the 1990’s. The construction industry, unlike the automotive industry, was not dealing with foreign competition. Instead the construction industry was dealing with a building boom in the United States and, as a result, the industry began to experience labor shortages. This was more the impetus for the construction industry to adopt lean tools rather than international competition.
Construction projects are complex. For every area that becomes leaner, resources, including labor, free up that allows the reallocation of that labor to other areas. One product category in particular has been an obstacle for contractors for decades is doors, frames, and hardware.
The typical welded hollow metal door, frame, and hardware installation requires hours of labor. In addition, the materials must be stored, moved (usually many times), damaged, repaired, replaced, and on and on. Contractors build in extra costs to cover all of these unnecessary wastes. And, beyond the door systems, drywall and sheetrock productivity can be negatively impacted by improper frame installations. This problem has existed for so long, the accepted industry paradigm is there is no better way other than to deal with the problems. Fortunately now there is a better way.
Customers/owners, architect, and contractor’s preferred solution would be a welded frame that installed after the walls are complete. Delivered as a “kit” (frame, door, and hardware) to the respective openings, the system would be installed in minutes by one laborer.
The Qwikinstall frame system can provide all of this. It is a two-piece interlocking welded hollow metal frame that installs after the walls are complete. It installs with one person, in six steps, in six minutes. No other welded frame installs faster than Qwikinstall and no other frame combines the strength and durability of welded frame with the benefits of installation after the walls are complete.
Data is available that shows the Qwikinstall welded hollow metal frame delivers benefits in labor, time, and cost. If you want to use your labor more efficiently, contact us today and start being more efficient (and cost effective) tomorrow.
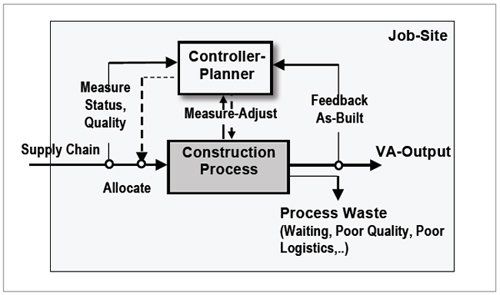